
If you are already a subscriber to The Process Cafe you will receive these update automatically in your RSS reader or inbox. If you don’t already subscribe you might wish to do so by clicking the RSS icon on the right of this post.
This post is going to focus on measuring your processes appropriately
There are two aspects to measuring your process. One is the concept of using measures to physically manage your process and the other is the detail of 'Comerford's Three Laws of Metrics'.
Ultimately the reason for managing your process is to understand what you do, how you do it and what you can do to make that process better. The last of these three items is the focus of measures. Measures are the way to understand in a quantitative way what is happening within your processes. By measuring a current state you are in a position to understand what the process is doing at the moment. By measuring a future state you then have comparison data which can be used to understand the effectiveness and efficiency of your process or process change. Effective and efficient processes are good. Ineffective and inefficient processes can then be identified and altered.
One of the fatal mistakes made in process projects is to implement a new process and then fail to measure it appropriately. The organisation then has no information or data to understand if the process is being used effectively or whether it has positively changed the outcome for the better. The logical extension of that is that any issues with the process are not captured, the process can then become inefficient and soon the benefit of making a process change is lost as workarounds and 'fixes' have to be made to solve efficiency problems with the process. At its worst a further project is created to then update the inefficient process and that falls into the same non-measured spiral as the previous one. The end result is a loss of user confidence in the process.
Putting measures into place is not easy. As you will read shortly when we discuss 'Comerford's Three Laws of Metrics' you will see that it is very easy to put a 'measure' in pace which fulfills the criteria of 'measuring' the process but does not actually provide any meaningful data for managing the process itself. Employees can dutifully spend hours every month collating and publishing the data on a dashboard or similar instrument and everyone can have a warm, fuzzy feeling that they are 'managing their processes'. This is very dangerous.
The one thing to be careful of when putting a measure in place for a process is to minimise the use of qualitative measures where possible. This is purely a matter of expediency. If you are measuring a process based on feedback from the users (and especially if you are using this to help appraise the people who are managing and running this process) then errors caused by human dissatisfaction with change are going to negatively influence the results. This is because putting a new process in will cause an element of change. A large number of people will dislike the change (regardless of whether it is good or bad) and a qualitative measure will highlight this dissatisfaction. Whereas if the element of change was removed from the satisfaction ratings the actual measure would be more useful. Unfortunately this doesn't happen.
Comerford's Three Laws of Metrics
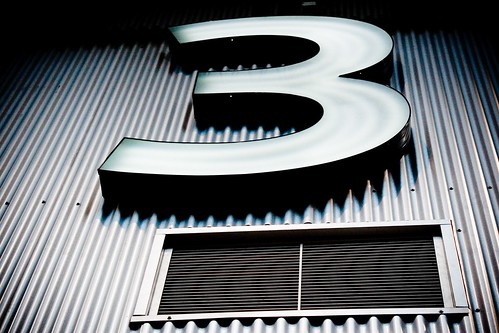
- Metrics for the sake of metrics are a waste of time:
- A metric which says 'I said I was going to do it and I did it' is also a waste of time:
- If you are going to gather metrics, at least have a way of feeding them back into the process to effect change:
Take a quantitative measure of "Number of approvals given in a processes". In my mind this is ultimately a wasteful measure. If the number of approvals is 1256, is this number relevant? What if it is 45? Or 223,678? None of these numbers mean anything as empirical measures of the process. Can you tell if a process is working effectively and efficiently as a result of reading the number 223,678? No you can't. Now if the measure was ''Percentage of all approvals that passed this stage first time" and the figure is 46% then THAT becomes a meaningful measure. Especially if a later analysis of the same measure identifies a decline to 35%. This is the point at which measuring the process produces meaningful information which can then be put back into the process to effect change (Comerford's Third Law)
Summary
Often neglected, measures are critical to understanding the effective and efficient running of your process. But proper care an attention must be paid to putting the appropriate measures in place. Without the appropriate measures (or with inappropriate measures), the benefit of measuring your process in the first place is lost.
On Monday we'll be looking at 'User Involvement' in our next post in this series.
For earlier posts in this series please click here:
Reminder: 'The Perfect Process Project' is still available. Don't miss the chance to get this valuable insight into how to make business processes work for you.
Click this link and follow the instructions to get this book.
All information is Copyright (C) G Comerford
See related info below